Alcast Company - The Facts
Alcast Company - The Facts
Blog Article
The 9-Minute Rule for Alcast Company
Table of ContentsThe Alcast Company DiariesThe Greatest Guide To Alcast CompanyA Biased View of Alcast CompanyAlcast Company Fundamentals ExplainedIndicators on Alcast Company You Need To KnowFacts About Alcast Company Uncovered
Chemical Contrast of Cast Light weight aluminum Alloys Silicon promotes castability by minimizing the alloy's melting temperature and improving fluidness throughout spreading. Additionally, silicon contributes to the alloy's stamina and put on resistance, making it useful in applications where resilience is essential, such as automobile components and engine components.It also boosts the machinability of the alloy, making it less complicated to refine into finished items. In this method, iron contributes to the total workability of light weight aluminum alloys.
Manganese adds to the stamina of aluminum alloys and improves workability (Aluminum Castings). It is typically used in functioned aluminum items like sheets, extrusions, and profiles. The presence of manganese help in the alloy's formability and resistance to fracturing during fabrication procedures. Magnesium is a light-weight element that gives stamina and effect resistance to light weight aluminum alloys.
The smart Trick of Alcast Company That Nobody is Talking About
It allows the production of lightweight parts with exceptional mechanical residential properties. Zinc enhances the castability of aluminum alloys and assists regulate the solidification procedure throughout spreading. It improves the alloy's stamina and solidity. It is typically located in applications where detailed shapes and fine details are needed, such as attractive spreadings and certain automobile parts.
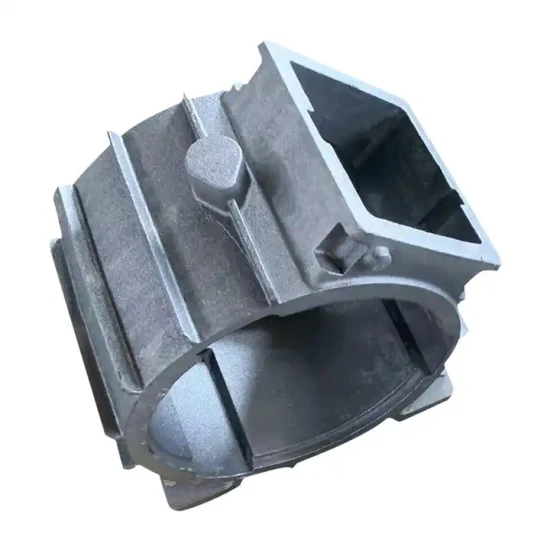
The primary thermal conductivity, tensile toughness, return toughness, and prolongation vary. Select ideal basic materials according to the performance of the target product created. Among the above alloys, A356 has the highest possible thermal conductivity, and A380 and ADC12 have the lowest. The tensile limitation is the contrary. A360 has the finest yield stamina and the highest possible prolongation price.
How Alcast Company can Save You Time, Stress, and Money.
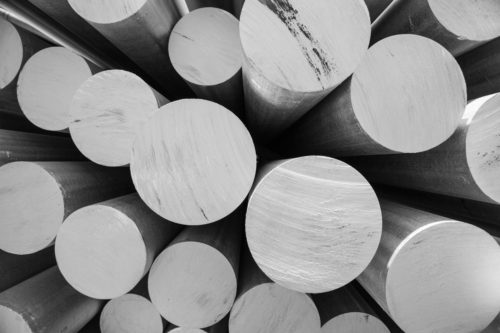
In precision casting, 6063 is appropriate for applications where intricate geometries and top notch surface area finishes are vital. check out here Instances include telecommunication rooms, where the alloy's premium formability enables streamlined and aesthetically pleasing styles while keeping architectural stability. In a similar way, in the Illumination Solutions sector, precision-cast 6063 components develop classy and effective lighting components that need complex shapes and good thermal efficiency.
The A360 displays exceptional elongation, making it perfect for complicated and thin-walled components. In accuracy spreading applications, A360 is appropriate for markets such as Consumer Electronic Devices, Telecommunication, and Power Devices.
Some Of Alcast Company
Its special residential or commercial properties make A360 a useful selection for accuracy spreading in these industries, enhancing product toughness and top quality. aluminum metal casting. Aluminum alloy 380, or A380, is a widely used casting alloy with a number of distinct features.
In precision spreading, light weight aluminum 413 radiates in the Consumer Electronic Devices and Power Equipment industries. This alloy's superior deterioration resistance makes it an exceptional choice for outdoor applications, making certain resilient, resilient items in the pointed out industries.
The Single Strategy To Use For Alcast Company
The aluminum alloy you select will considerably influence both the casting process and the residential properties of the last item. Because of this, you should make your choice meticulously and take an enlightened approach.
Figuring out the most appropriate aluminum alloy for your application will imply weighing a wide array of characteristics. The initial group addresses alloy attributes that impact the manufacturing process.
Fascination About Alcast Company
The alloy you select for die casting straight affects a number of elements of the casting procedure, like exactly how very easy the alloy is to deal with and if it is prone to casting flaws. Hot fracturing, also recognized as solidification breaking, is a typical die casting defect for light weight aluminum alloys that can result in inner or surface-level tears or fractures.
Particular aluminum alloys are a lot more at risk to hot breaking than others, and your choice needs to consider this. It can harm both the cast and the die, so you ought to look for alloys with high anti-soldering residential properties.
Deterioration resistance, which is already a significant feature of aluminum, can vary considerably from alloy to alloy and is a crucial characteristic to consider depending upon the ecological problems your item will be subjected to (Foundry). Use resistance is an additional home frequently looked for in light weight aluminum items and can separate some alloys
Report this page